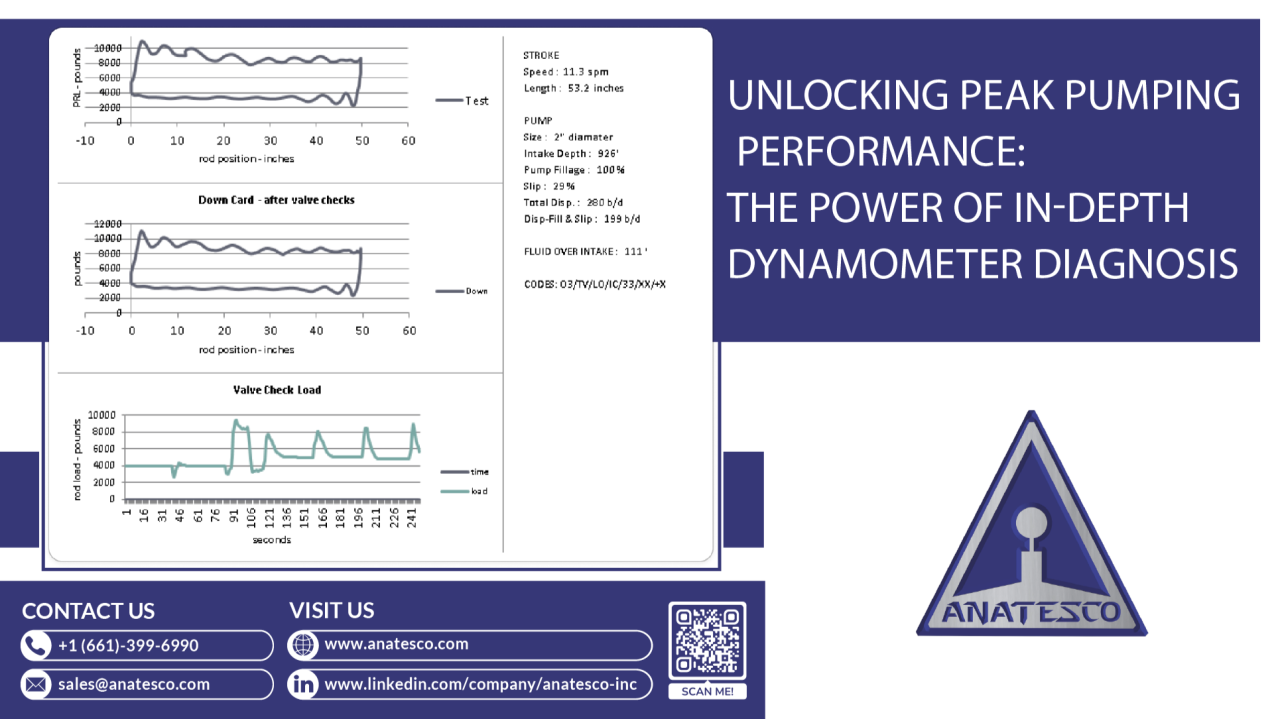
Unlocking Peak Pumping Performance: The Power of In-Depth Dynamometer Diagnosis
Beyond the Surface: Diagnosing and Optimizing Well Performance with Advanced Dyno Testing
Why Surface-Level Analysis Isnβt Enough?
Dynamometer testing has long been a critical tool in artificial lift optimization, helping engineers diagnose rod pump efficiency, fluid movement, and mechanical integrity. However, standard diagnostics often fall short in identifying the deeper issues affecting well performance.
A basic dyno test may highlight pump-off conditions or counterbalance inefficiencies, but an in-depth dynamometer diagnosis offers a granular view of well dynamics, uncovering hidden inefficiencies, valve behavior, and subsurface flow restrictions that traditional tests fail to detect.
π° The Role of Advanced Dynamometer Testing in Well Optimization
A dynamometer test measures the load and displacement of the polished rod throughout a pump cycle, helping engineers pinpoint problems with rod lift systems. While traditional dyno cards provide insights into pump fillage, gas interference, and mechanical wear, advanced dynamometer diagnosis incorporates additional cutting-edge techniques to maximize efficiency:
β High-Resolution Load Profiling β Capturing microvariations in pump stroke mechanics for enhanced diagnostic accuracy.
β Dynamic Fluid Level Analysis β Assessing reservoir inflow, optimizing production rates, and detecting liquid loading issues.
β Vibration and Torque Evaluation β Identifying side loading, excessive torque, and downhole mechanical strain.
β Real-Time Valve Performance Checks β Detecting flow restrictions, valve leaks, and seating issues before they reduce efficiency.
β Accurate Pump Slip Measurements β Measuring fluid slippage between the pump plunger and barrel, allowing for precise tuning beyond what standard pump-off controllers can achieve.
β Automated Data Integration β Comparing dyno test results over time to track performance trends, equipment wear, and failure risk.
π― Key Benefits of In-Depth Dynamometer Diagnosis
π Early Failure Detection β Predicting mechanical failures before they cause costly downtime.
π Optimized Pump Efficiency β Adjusting stroke length, speed, and counterbalance settings for maximum production.
π‘ Better Well Diagnostics β Gaining a clearer picture of fluid levels, gas interference, and wellbore dynamics.
π Data-Driven Decision Making β Utilizing AI-assisted analytics for trend recognition and predictive maintenance.
π οΈ Proactive Valve Management β Addressing subsurface valve issues early, extending the lifespan of downhole components.
βοΈ Precision Pump Calibration β Using high-accuracy slip measurements to fine-tune pump configurations, reducing energy consumption and increasing efficiency.
π Case Study: Diagnosing the Root Cause of a Pumping Issue
Problem: Erratic Production Declines Despite Normal Surface Readings
An operator in the Permian Basin experienced unexpected production declines across multiple rod-pumped wells, despite stable surface-level data. Traditional diagnostics showed no immediate signs of pump-off conditions, leaving the root cause unknown.
π¬ Advanced Dynamometer Analysis Revealed:
β‘οΈ Gas interference was causing partial pump fillage, significantly reducing liquid recovery rates.
β‘οΈ Polished rod side loading indicated a misalignment issue, leading to uneven wear and increased energy consumption.
β‘οΈ Fluid level tracking revealed rapid reservoir drawdown, requiring adjustments in artificial lift strategy.
β‘οΈ Valve performance inconsistencies detected in real time pointed to a developing obstruction restricting flow.
β‘οΈ Excessive pump slip β identified via high-resolution load profiling β signaled the need for pump component recalibration.
π The Results:
β 25% increase in production after optimizing gas management and pump timing.
β Extended rod pump lifespan through realignment and counterbalance adjustments.
β Reduced maintenance costs by preventing a premature pump failure.
By leveraging advanced dynamometer diagnosis, the operator was able to make precise adjustments, restore efficiency, and extend the operational life of their artificial lift system.
π€ The Future of Dynamometer Diagnostics: AI-Driven Optimization
As machine learning and AI-powered analytics reshape oilfield diagnostics, dynamometer testing is evolving beyond traditional methods. Emerging technologies are introducing real-time monitoring, remote diagnostics, and predictive failure modeling, allowing for proactive intervention rather than reactive troubleshooting.
πΉ Automated Anomaly Detection β AI can now identify small deviations in load patterns, predicting potential failures weeks in advance.
πΉ Remote Well Monitoring β Cloud-connected dynamometers provide real-time performance data, allowing engineers to optimize lift settings remotely.
πΉ Predictive Maintenance Modeling β AI-driven simulations can forecast rod pump wear rates, helping operators schedule targeted maintenance instead of reactive replacements.
By combining real-time diagnostics with predictive analytics, operators can dramatically extend equipment lifespan, lower energy costs, and improve well performance.
π’ Unlock Your Wellβs Full Potential with Anatesco
At Anatesco, we specialize in precision dynamometer diagnosis, helping operators move beyond surface-level analysis and into data-driven optimization. Whether youβre troubleshooting rod lift inefficiencies, gas interference, or pump calibration, our advanced dyno testing solutions provide the insights you need to maximize production and minimize downtime.
π§ Connect with Anatesco today to explore how in-depth dynamometer diagnostics can enhance your well performance.
π Contact us:
π§ Email: Fred@anatesco.com π± Call us: +1 (661)-399-6990
π Website: www.anatesco.com π Connect with us on LinkedIn: Anatesco Inc.